Central Plants & Infrastructure
Fanning, Fanning & Associates Inc.
Covenant Hospital Plainview is a regional hospital located in Hale County, Texas. The original facility was built in 1968 and contains 165,000 square feet of floor space. The hospital’s original HVAC system consisted of an all-air system except for the patient rooms. The air handling systems were four-pipe, served by heated and chilled water which was generated in a central plant located adjacent to the main building. Most of the air handlers were located in a ground-floor equipment room. Hot water was generated from steam in the plant and piped to the air handling units. Patient rooms were served by the original four-pipe fan coil units in each room adjacent to the toilets. Dedicated air handling units served fresh air to the patient rooms.
FF&A was commissioned to do an assessment of the HVAC system which recommended that the hospital upgrade the mechanical components to bring the facility back to where it can provide an ideal environment for the patients and staff.
FF&A resulted project to remedy the facility's inadequate HVAC system. This resulted in the replacement of the air handling units, the fan coil units, as well as much of the hot and chilled water lines which were corroded. The complexity of the project was increased by the fact that the hospital had to remain operational throughout the construction process. Weekly meetings were conducted to coordinate this complicated process. Special attention by the A/E team was paid to Interim Life Safety Measures as well as infection control. The facility now has a functioning, state-of-the-art system that meets or exceeds all regulations regarding hospitals.
Client:
Covenant Health Plainview

Year Completed:
Professional Services: 2011
Construction: 2011
Project Size: 165,000 SF
Project Cost: $9.5 M
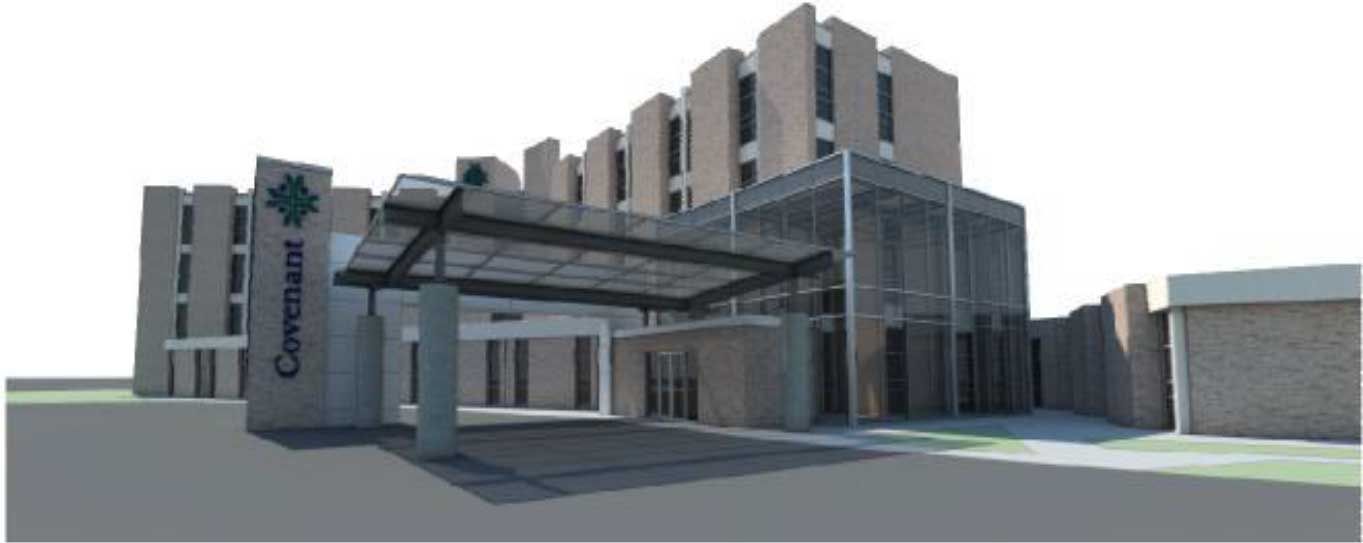
USDA AMS CTP purchased the building from the Lessor in 2017. At that time, the building was 20 years old and required renovations. The primary deficiencies at that time were a leaking roof, a non-functional chiller, an insecure back lot, and air handling equipment in need of replacement. In four separate contracts, Fanning, Fanning & Associates designed the Phase 1 project, which included fencing and paving at the rear of the building, with a second entry into the back lot of the building. Also included were air compressors, an HVI vacuum pump, a temperature control system replacement, a water treatment system replacement, and associated electrical work. Phase 2A is out for bid and int includes potential replacement of air handlers, reheat coils, Data Room HVAC, Boiler feed system, and replacement of the main electrical switch. The roofing project was recently completed by KWA, the team’s roofing consultant. The bid packages for these building improvements were configured for maximum flexibility, allowing USDA CTP to pick and choose desired improvements based on cost and schedule.
Client:
USDA AMS, Cotton &Tobacco Program
Year Completed:
Professional Services: 9/2019 - Current
Construction: 3/2022 - Current
Project Size: 15,000 SF
Project Cost: $2.7M
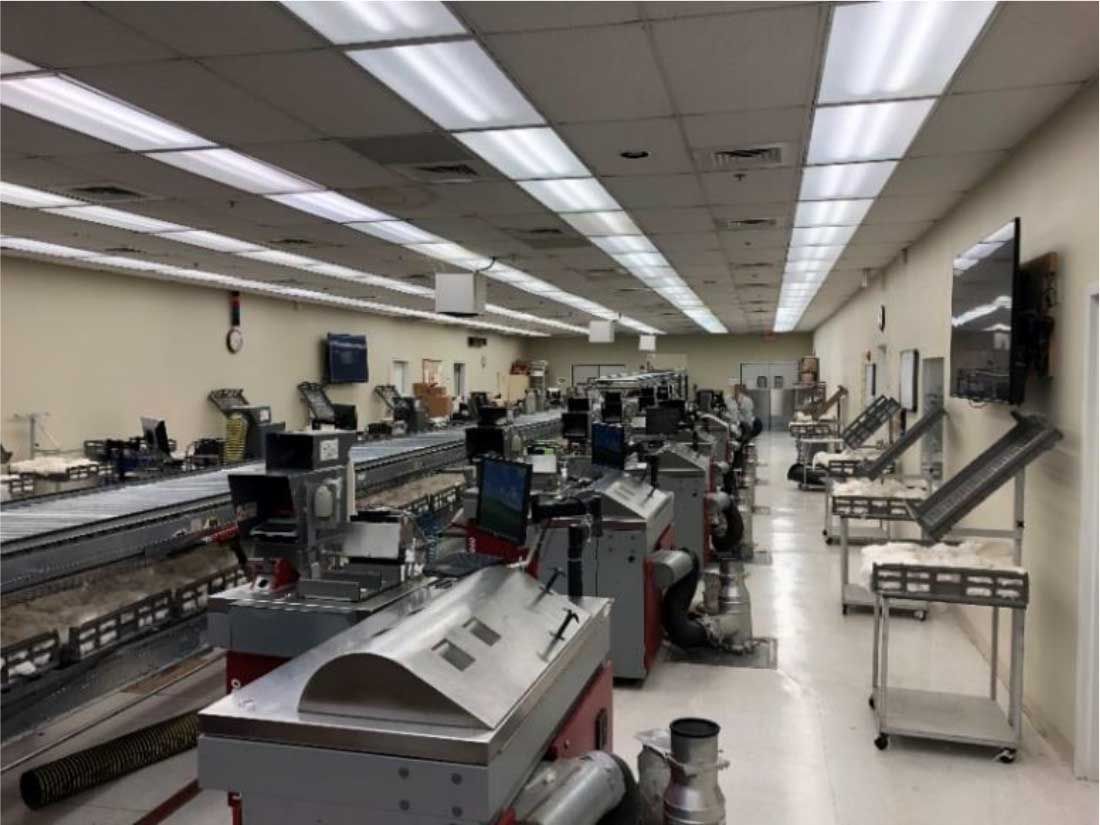
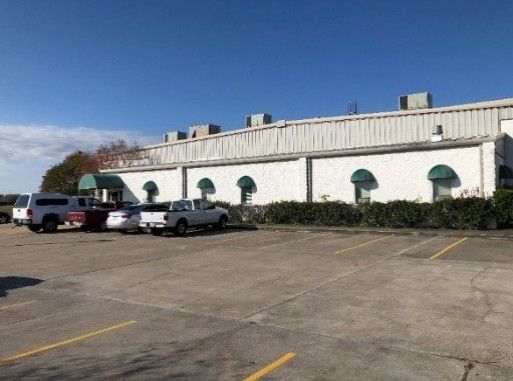
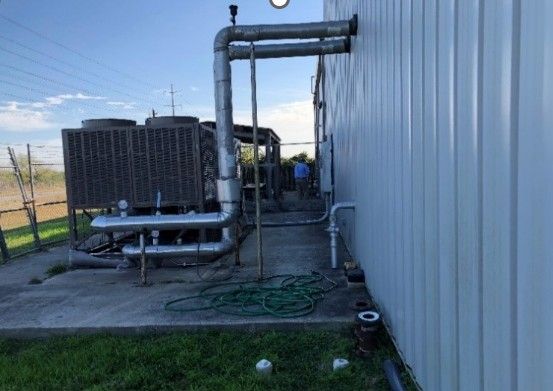
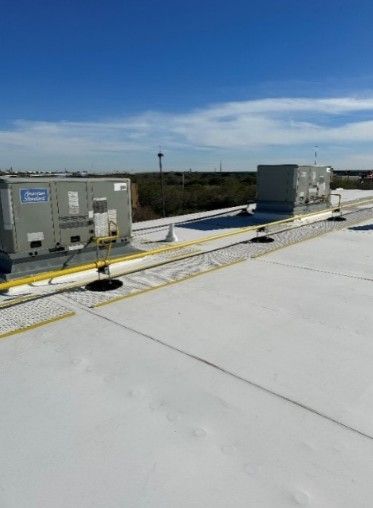
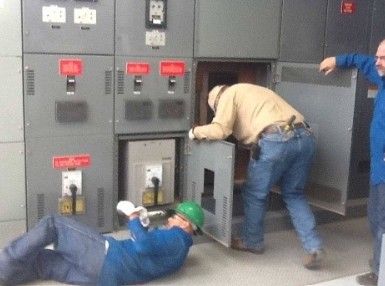
The Federal Pacific Electric (FPE) switchgear at CHACP2 was installed when the building was constructed in the 1970’s. Since FPE has been out of business for 20+ years with parts unavailable for the aging switchgear, there was a compelling need to replace the switchgear with current “state-of-the-industry” equipment.
CHACP2 provides steam and chilled water utilities to TTU Health Sciences Center (HSC) and University Medical Center (UMC) along with backup emergency power to HSC. The challenge was to do a total replacement of the switchgear while keeping CHACP2 in operation. For this reason (and budgetary constraints), a plan was developed to perform the replacement in four phases.
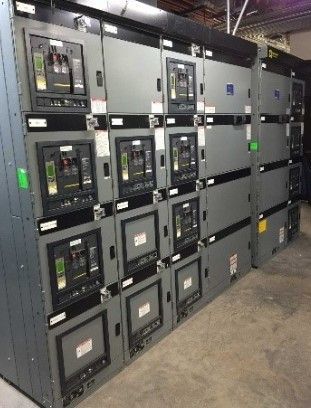
Phase 1 involved the installation of some temporary feeders to clear the space and the construction of a new electrical mezzanine room in the basement immediately below the existing electrical room. Phases 2 and 3 involved the installation of new distribution switchgear, busduct, and motor control centers in the new electrical room while keeping the existing equipment operational. New variable frequency drives (VFDs) were installed for the chilled water pumps and condensing water pumps and the VFDs for the cooling towers were relocated to the new electrical room. Phase 4 involved the extension of the mezzanine electrical space and the replacement/relocation of the backup emergency transfer switches, emergency panelboards, and related emergency equipment. Every piece of major electrical equipment and associated wiring was replaced. The project was completed in 2016.
CHACP2 electrical system was designed to permit the plant to continue in full operation in the event of failure of any major electrical component such as one of the service transformers, one of the incoming busducts, or one of the main circuit breakers. In the event of a total power failure, the existing 2600 KW emergency generator can be switched to keep the plant operational.
In conjunction with this project, CHACP2 is also upgrading the control and monitoring system with “state-of-the-industry” controls. 
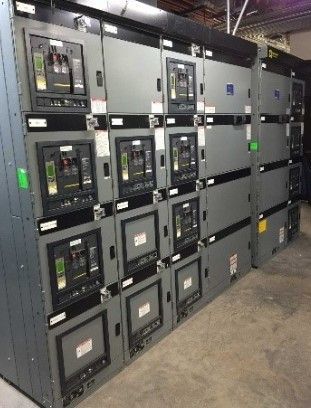
Client:
Texas Tech University - Utilities
Year Completed:
Professional Services: 2015
Construction: 2016
Project Type: Electrical Switchgear Replacement
Project Cost: $3.4M
The Headquarters facility for USDA AMS Cotton and Tobacco was constructed in Memphis, Tennessee in 1992-1994. The facility includes CTP Administration, Memphis Classing Lab, QC Lab, and research and development of automation and cotton standards. As the equipment began to approach the end of its useful life of 25-30 years, some equipment was failing, including chillers, cooling towers, heat exchangers, boilers, and air compressors. It was critical that the solicitation of replacement equipment be configured to allow CTP maximum flexibility in project duration, efficiency, and cost. The contract documents were divided into bid packages that allowed CTP to consider the life cycle cost of the replacement equipment. Ultimately, one 200-ton chiller, one 200-ton cooling tower, one 90 HP boiler, and a 200-ton plate frame heat exchanger were replaced. The project was awarded within the available budget and within an acceptable schedule in June 2023. The project included an electrical design to support the replacement equipment. The project is under construction and will lead to greater reliability for CTP’s mission.
Client:
USDA AMS, Cotton &Tobacco Program
Year Completed:
Professional Services: 2023
Construction: 2023
Project Size: 80,000 SF
Project Cost: $1M
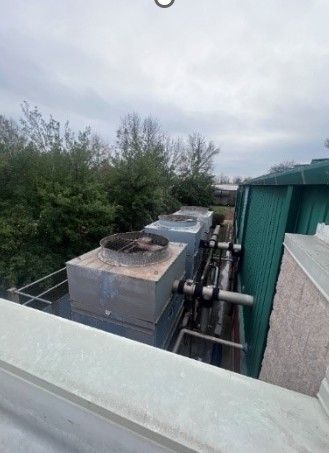
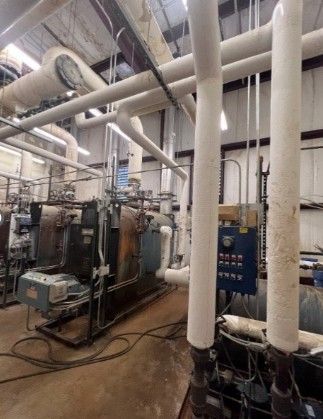
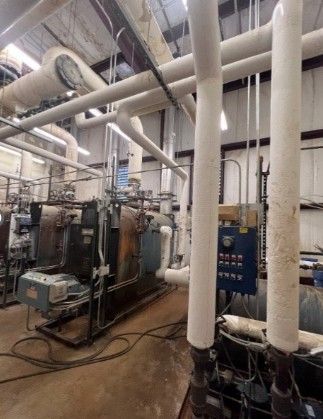
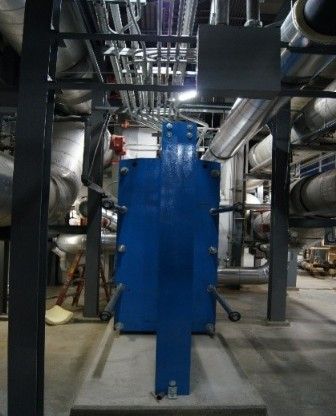
FF&A designed the installation of two 1500-ton plate frame heat exchangers for Plant 1. The units were rated to deliver 8 degree temperature difference (38-46 deg. F on the cold side and 49 to 41 deg. F. on the hot side), with a three-degree approach. The design integrated an automatic backflush of the condenser water side of the heat exchanger and included a detailed piping design with valves, controls, and strainers. FF&A was involved in the project from the earliest stages, at inception in the fall of 2010, through design in the spring of 2011 and installation in the summer of 2011. FF&A considered installation space, rigging, piping connections, cost, and demolition of four existing chilled water pumps. The design was completed on an accelerated schedule and the installation was successful.
Upon testing the plate frame heat exchanger that was submitted and installed, it was found to be deficient. A lack of response by the manufacturer brought the process to a near standstill. FF&A worked diligently on behalf of Texas Tech with the manufacturer to bring them to the table to correct the deficiencies in capacity. At no additional fee, FF&A worked with the manufacturer and Texas Tech to negotiate a solution that was implemented successfully by the manufacturer. FF&A has been a fierce advocate for Texas Tech on all projects is involved in, regardless of the time or effort involved.
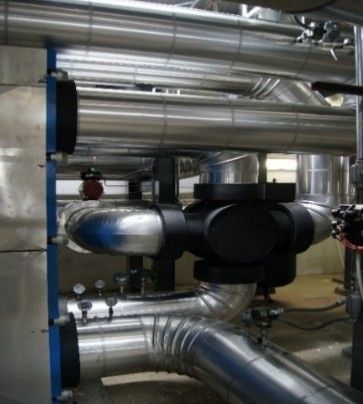
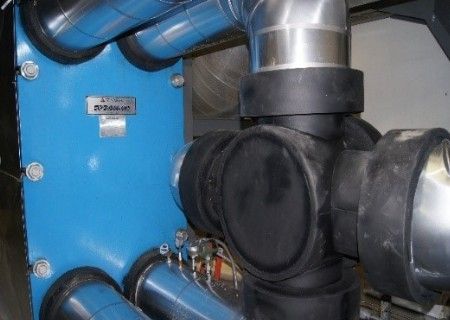
The upgraded plate frame heat exchangers went online in the summer of 2013, and testing revealed that they outperformed the specifications. There are weeks in the winter when Texas Tech provides chilled water to the campus exclusively through these heat exchangers without ever starting a chiller.
Client:
Texas Tech University - Utilities
Year Completed:
Professional Services: 2011
Construction: 2013
Project Type: Major Equipment Installation in CHACP1
Project Size: 3,000 tons Refrigeration
Project Cost: $800,000
Share On: