Federal & Military
Fanning, Fanning & Associates Inc.
Dormitory Building 1002, Fort Sam Houston (San Antonio, TX)
In 2010, Fanning, Fanning & Associates joined the design team of Parkhill, Smith, and Cooper and Contractor Harrison, Walker, and Harper and Federal Program Integrators (FPI) for the design and renovation of a six-story dormitory. The project area was approximately 70,000 square feet, with a cooling load of approximately 155 tons. The project included the complete replacement of the outdoor air ventilation system. A new dedicated outside air system was added for each of the five floors. The new system provided 48-degree F. dewpoint outside air to each dormitory room by supplying glycol/water from an air-cooled chiller. Existing water-source heat pumps were relocated to closets accessible for maintenance from the main corridors, instead of from inside the dorm rooms. A shared toilet was demolished and individual toilets were added to serve each dorm room. All plumbing and HVAC piping risers were replaced under the project. The electrical system, CATV, telephone, data, and fire alarm systems were renovated. The goal of the project was to improve comfort and reduce indoor relative humidity to acceptable levels. The design included compliance with ETL-04-3 Design for Prevention of Mold. The project is currently under construction.
Client: Parkhill
Year Completed:
Professional Services: 2010
Construction: 2012
Project Size: 70,000 SF
Project Cost: $16.6M
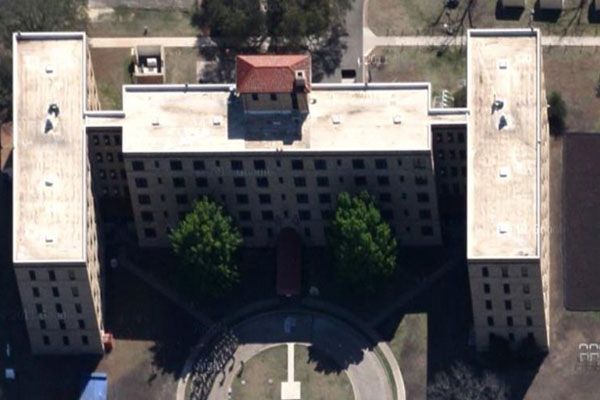
1400 Dorms, Lackland Air Force Base (San Antonio, TX)
In 2010, Fanning, Fanning & Associates joined the design team of Parkhill, Smith and Cooper Harrison, Walker, and Harper and Federal Program Integrators (FPI) for the design and renovation of three dormitories at Lackland AFB. Each dormitory was approximately 25,000 square feet, with a cooling load of approximately 55 tons. The project included the complete replacement of the HVAC system and most of the plumbing system. The electrical system, CATV, telephone, data, and fire alarm systems were renovated. The goal of the project was to improve comfort and reduce indoor relative humidity to acceptable levels. The mechanical system consisted of four-pipe fan coil units. An existing district heating and cooling plant supplied chilled and heating water to the building. The design included compliance with ETL-04-3 Design for Prevention of Mold and included a dedicated outside air system for each dormitory. The project is currently under construction.
Client: Parkhill
Year Completed:
Professional Services: 2011
Construction: 2012
Project Size: 75,000 SF
Project Cost: $11.45M
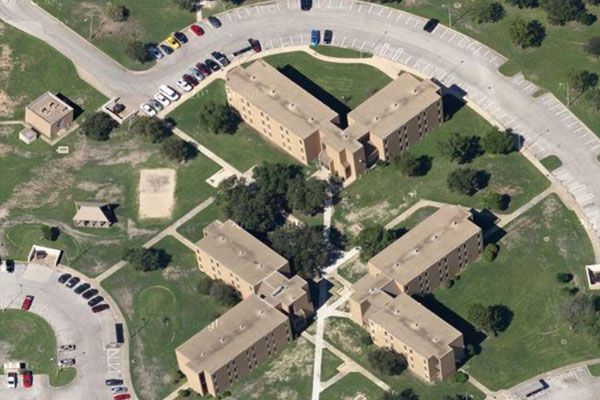
Rehabilitation of Dormitories (3206, 3210) and Laundry (3208) Renovation (Goodfellow Air Force Base, TX)
The initial scope of work for buildings 3206, 3210, and 3208 included full replacement of interior finishes including gypsum board and all mechanical and plumbing systems. During demolition, black mold was identified and the project was delayed to obtain additional funding. The project was phased by building and by floor to help minimize the impact of the unknown mold issues. Additionally, the exterior concrete circulation areas were not properly sloped to provide positive drainage. Moisture pooled onto the structural slabs and through years of freeze/thaw, the concrete degradation became so severe reinforcement steel became exposed. Rainwater was also coming into the individual living units as a result. The exterior walkways were needle hammered to remove the spawling concrete to prepare the surface for a new topping slab providing positive drainage. Mechanical and plumbing systems were replaced in their entirety to provide dehumidification to meet ETL 04-3 Design Criteria for Prevention of Mold in Air Force Facilities and to meet ASHRAE 90.1-2007 Indoor Air Quality.
Client: US Army Corps of Engineers
Year Completed:
Professional Services: 2015
Construction: 2017
Project Size: 130,000 SF
Project Cost: $9M
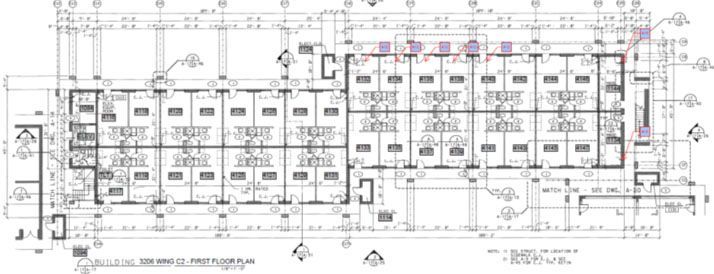
Army Community Service Center - HVAC System Replacement - Building 920, (Fort Polk, LA)
The Army’s 19,000 gsf Community Service Center at Fort Polk had been evacuated due to mold growth and water intrusion. The project scope included closing gaps in the building exterior, and completely replacing the HVAC system in the building. The source of some of the mold growth was the existing HVAC system's inability to dehumidify the outside air to prevent mold growth. To prevent further damage, the outside air dampers on the building had been closed. The result of these circumstances was a building that was not inhabitable due to mold and stagnant conditions.
The existing multizone air handling unit system, air-cooled chillers, and gas-fired boiler were replaced, along with all piping and ductwork. The heart of the new system was a dedicated outside air system unit (DOAS). This unit included exhaust and supply fans, and a dual-wheel design, with total energy recovery and a passive dehumidification wheel. This unit delivered air at a dewpoint of less than 50 degrees, effectively solving the high-humidity problem. The system met ITG FY05-02, NAVFAC Humid Area HVAC Design Criteria. Air handling equipment included two new single duct air handling units designed to serve single duct VAV boxes with hydronic reheat and DDC Box controllers. New air-cooled packaged chillers were added (two nominal 40-ton units), along with a condensing boiler. The building automation system was replaced entirely, and the number of control zones in the single duct hydronic reheat system virtually doubled. The design of the air handling systems ensured a positive building pressure using airflow monitoring stations to track outside air and exhaust entering and leaving the building. Demand-controlled ventilation was utilized for four large muster areas that were intermittently occupied. The system as installed met ASHRAE 62.1, Ventilation for Acceptable Indoor Air Quality. The result of the project was the solution to the mold and sick building problems. The design team was able to solve the problems and create healthy, productive spaces for Community Service Center Staff.
Fanning, Fanning & Associates partnered with HWH and NAVAR to design and install these renovations.
Cost: $5M
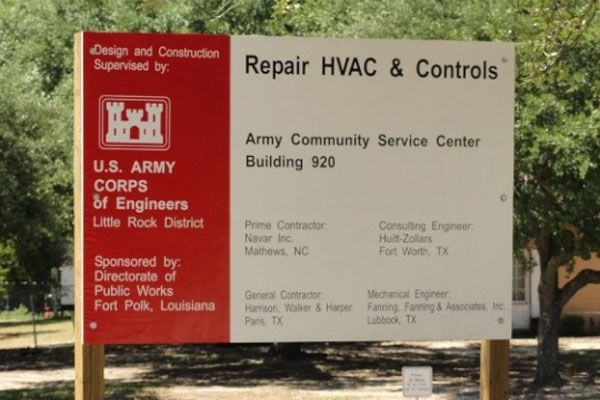
Renovation of Buildings 4168 & 4205, US Army North, Fort Sam Houston (San Antonio, TX)
These projects renovated a 9,000 gsf building (4168) that housed storage and office space in the Company and Battalion Headquarters for US Army North at Fort Sam Houston. The renovation provided all new finishes for the building. The renovation was phased such that the existing office area remained in use during construction. All systems serving Company and Battalion Headquarters were segregated and served from separate sources. The building's HVAC system consisted of split system heat pumps, approximately 25-ton capacity building. The project also included the renovation of two bays of a warehouse for the storage of mobile command center vehicles. Overhead doors were replaced, and new lighting, power, and fire protection systems were provided along with the finishes in the space. Infrastructure was added to support the long-term storage and battery charging for the mobile command center vehicles. The project was successfully completed in 2011.
Client: US Army Corps of Engineers
Year Completed:
Professional Services:
Construction: 2011
Project Size: 9,000 SF
Project Cost: $2M
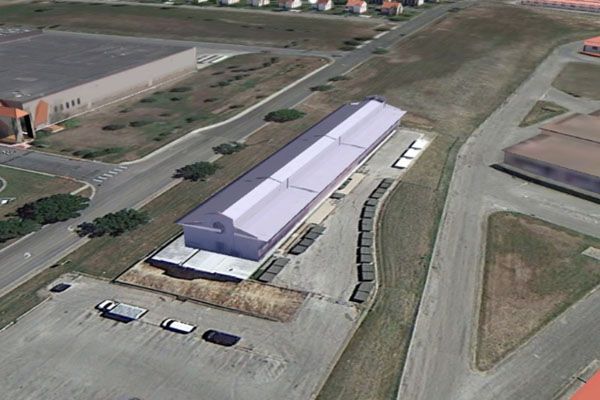
Share On: