Testing & Research Labs
Fanning, Fanning & Associates Inc.
FF&A designed the HVAC, Plumbing, Fire Protection, Life Safety, Electrical: Lighting, Power, and Communications systems for the Experimental Sciences Research Lab Building. The new building provides needed state-of-the-art support and analytical research facilities to support the mission of this project and the larger campus science community. It also provides essential research laboratory space characterized by an open “Institute” environment that emphasizes an interdisciplinary research approach. The lab spaces include a lab airflow control system that ensures negative pressure relationships in contaminated or laboratory areas. The BSL-3 shared containment lab includes controls that allow the staff to individually monitor and control the temperature in each animal space. The building also includes a seminar room equipped for computer connections and designed for a quiet (NC25) sound criteria environment. Our involvement has been continuous in retrofit and renovation since the lab was opened including the A-Shell completion.
Client:
Texas Tech University / CO Architects
Year Completed:
Professional Services: 2005
Construction: 2006
Project Size: 127,810 SF
Project Cost: $46.9M
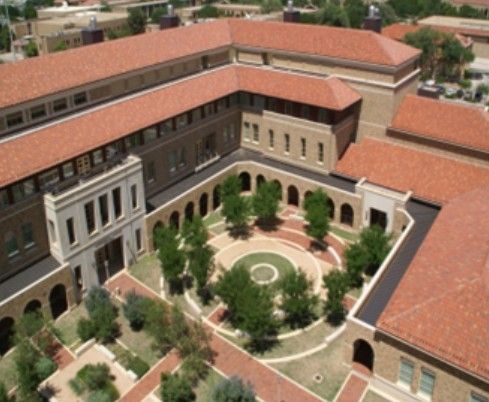
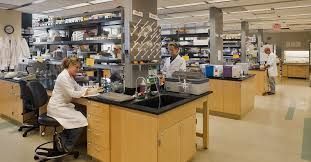
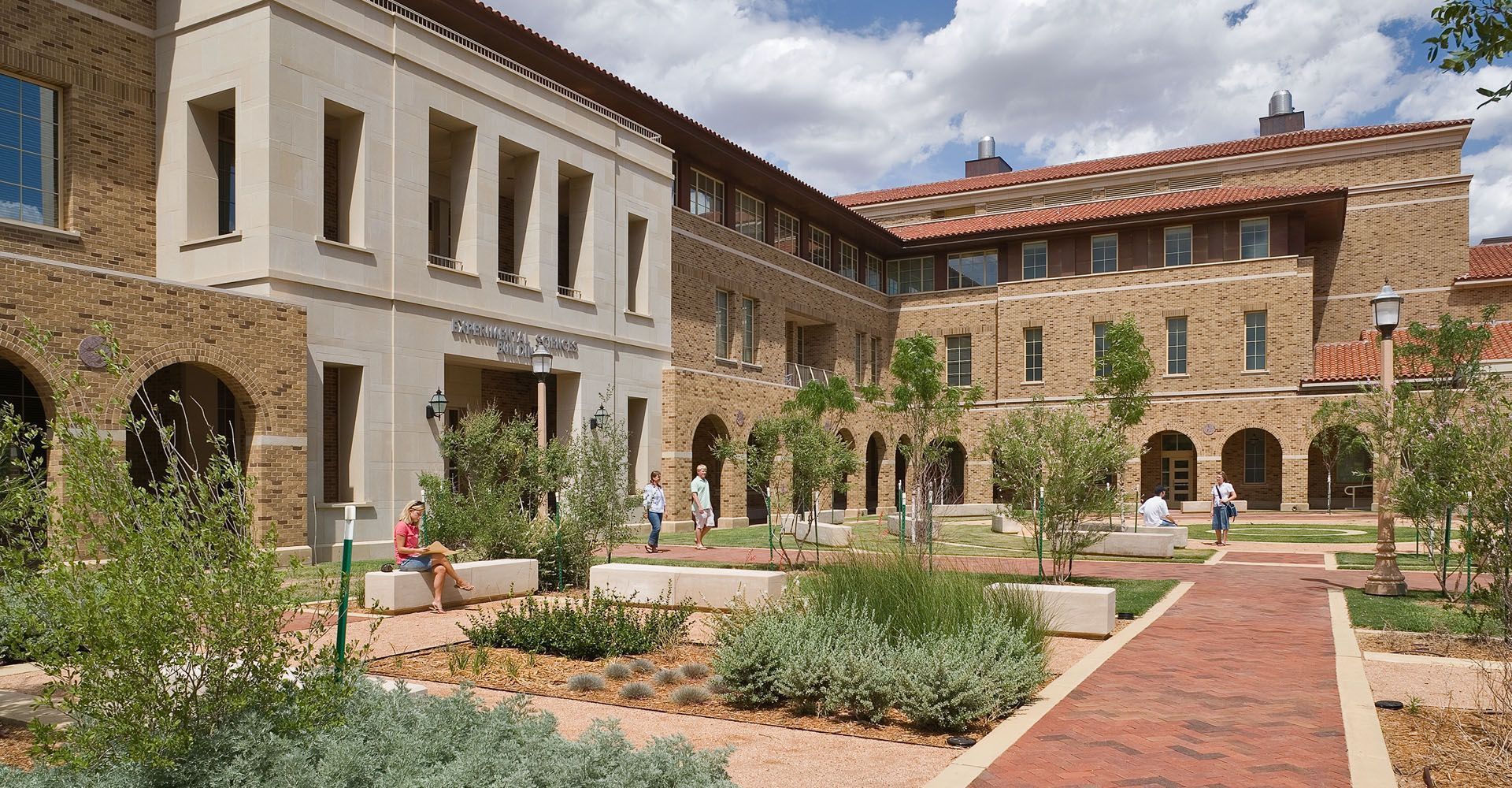
FF&A designed the HVAC, Plumbing, Fire Protection, Life Safety, Electrical: Lighting, Power & Communications systems for the Maddox Engineering Research Center. The renovated building provides a home for the WCOE Maddox Chairs. The building includes advanced specialized material identification lab equipment in the basement and wet and dry labs on the first and second floors. The building features manifold exhaust, heat recovery, and variable air volume systems. The lab spaces include a lab airflow control system that ensures negative pressure relationships in contaminated or laboratory areas. The building is equipped with energy-efficient lighting and an emergency generator. The project utilized the building built for Mass Communications in the 1970s which was demolished down to the exterior walls and rebuilt for its new function. The project budget was $29 million, with the mechanical, plumbing, and electrical totaling approximately one-third of that amount. This project demonstrated FF&A’s ability to design infrastructure including HVAC, Plumbing, and Electrical to support equipment such as atomic force microscopy (AFM), gas chromatography (GC), confocal microscopy, centrifuges, high-performance liquid chromatography (HPLC), atomic absorption autosamplers and spectrometers (AA), polymerase chain reaction (PCR) equipment, and nuclear magnetic resonance (NMR) spectroscopy.
Client:
Texas Tech University / Western Builders / Condray Design Group
Year Completed:
Professional Services: 2015
Construction: 2016
Project Size: 79,039 SF
Project Cost: $29M
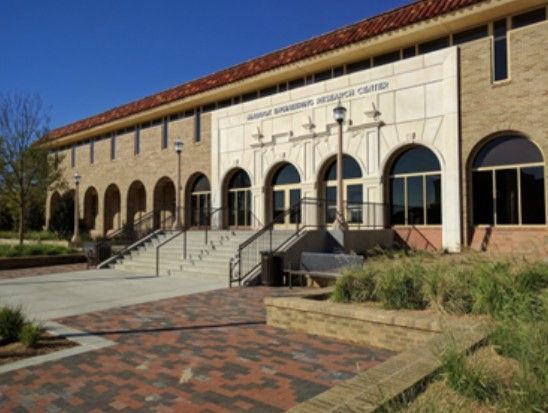
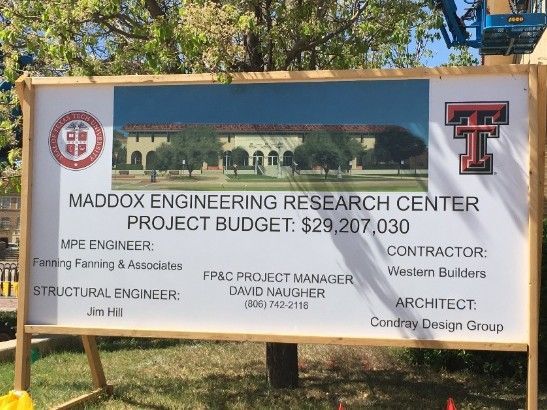
The Lubbock Cotton Classification Complex (CCC) was opened in the fall of 2022 and is the flagship of all Cotton Classing Facilities. Owned and operated by the USDA AMS CTP, the facility is located on the campus of Texas Tech University. The partnership was shepherded by the design team, including initial introductions, to the signing of the cooperative agreement, allowing CTP to build on the Texas Tech Campus. By volume, Lubbock CCC will class up to five million bales per year, approximately 20% of the US cotton crop. The classing lab is completely automated with 24 high-volume instruments (HVI), automated cotton conveyance, and flexible space for expansion or R&D. The lab serves as a platform for collaboration between CTP, cotton producers, and higher education and research in fiber technologies.
The project, like all other CTP ASTM facilities, is designed to maintain 70 degrees F, plus or minus 1 degree, and 65% relative humidity, plus or minus 2% RH. Fanning, Fanning & Associates, and its design partners have designed all labs to better than this tolerance, which allows consistent and continuous classing of samples for cotton producers.
The project includes many innovative features, including:
- Artwork and furnishings that reflect the unique history and character of cotton classing.
- YETI Cooler Construction – ICF Block around ASTM Spaces for tight construction.
- High Efficiency Lighting including daylighting, motion detection, and LED fixtures.
- Energy efficient HVAC system for Office Area – variable refrigerant flow HVAC system is the most efficient stand-alone system, providing 50% improvement over conventional systems.
- Heat Recovery – 150-ton heat recovery chiller that uses the heat of rejection to provide required reheat water to maintain ASTM conditions.
- Fee Cooling – a waterside economizer that uses direct heat exchange to provide cooling in the fall and winter months when most of the cotton is classed.
- Energy efficient heating system, consisting of a condensing boiler.
- High-efficiency filtration – three stages of filtration
- Control components to achieve superior control tolerances, energy monitoring, and real-time rotating display of ASTM conditions.
- All aspects of LEED Silver goals were met in the project.
Client:
USDA AMS, Cotton & Tobacco Program
Year Completed:
Professional Services: 2018
Construction: 2022
Project Size: 34,680 SF
Project Cost: $14.7 M

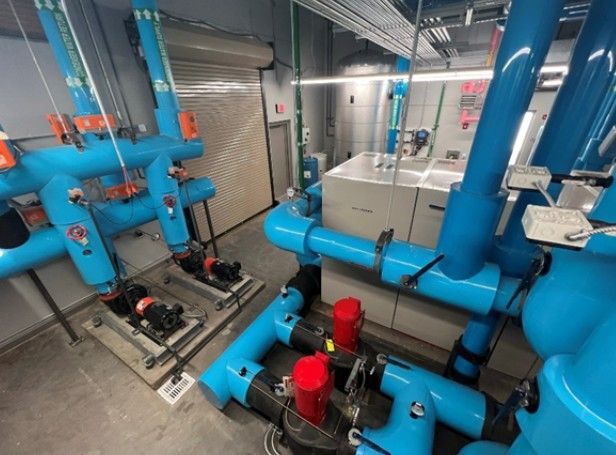
As the second lab to be designed from scratch to use automated classing techniques, the Raleigh, North Carolina USDA Cotton Classing Lab was designed under the current CTP IDIQ contract by the FF&A Team. It is unique in that it will house the only USDA Tobacco Training Facility in the nation. Through the design charette held at the CTP Headquarters in Memphis, ideas for the lab were consolidated into a schematic plan. This project presented unique challenges in design because, in addition to seasonal and permanent staff, the Tobacco Program offices needed to be incorporated into this facility. Through careful design, building efficiency was optimized by sharing all services and spaces that could be shared.
Particular care was taken in the design of the building envelope to contain the high humidity involved with conditioning cotton and tobacco samples. ICF Block (Styrofoam/concrete blocks will form the vapor barrier for both cotton classing and tobacco training. The tobacco training room is designed to be used as a flexible space that will be convertible to cotton classing or hosting meetings and lectures for large groups. The FF&A team paid particular attention to the design of all aspects of the building envelope to reduce condensation to extend the life of the facility. All of the key provisions for the Lubbock lab were incorporated into the design of the Raleigh lab, including the visionary partnership with higher education for research and teaching. The FF&A / A&E team has advocated for the CTP with North Carolina State University to explore a partnership in the future.
Building systems have been designed with overlapping features to allow for very tight temperature and humidity control. For the classing lab, the ASTM-regulated spaces will be controlled to 70 degrees. F., +/- 1 deg. F., and 65% RH, +/-2% RH. The tobacco training room is used to hydrate tobacco samples that have been kept in cold storage, and during this process, the room is maintained at the environmental conditions of 72 deg. F., +/-1 deg. F., and 85% RH, +/- 4%RH. Control techniques perfected over the 32-year relationship between CTP and FF&A are essential to keep the conditions within tolerance. The tobacco training room can be maintained to the ASTM cotton classing condition with a flip of a switch. The HVAC system consists of water-cooled, heat recovery chillers that provide redundancy, reliability, and a source of heat recovery that is used in the process of reheating coils. Plate frame heat exchangers are utilized in conjunction with one of the two stainless steel cooling towers to provide chilled water utility during the winter months without running refrigeration compressors. Condensing boilers provide “topping” for the reheat temperature when needed. The office area is served by a variable refrigerant volume HVAC system, which is the most efficient available for the office function. In every system throughout the building from HVAC controls to Lighting controls, from daylighting to free cooling, the watchword of the design is Efficiency.
One of the features of both the Lubbock and Raleigh facilities is an energy management overlay that has been designed to be added in the future. The overlay will allow an energy manager at Memphis headquarters to view the condition performance as well as the energy performance of each CTP facility. This feature will allow a consistent view of all the labs in the CTP program from one location while permitting the control systems in the various locations to be installed by diverse vendors who have strength of maintenance and service in each unique locale. This innovation has been specified by the FF&A team in both of these state-of-the-art cotton classing labs.
Client: USDA AMS, Cotton & Tobacco Program
Design Only: Not Constructed
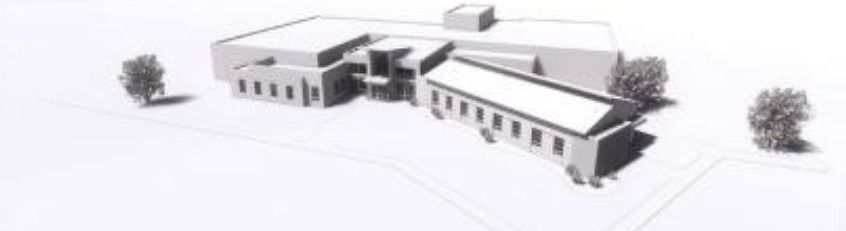
The USDA AMS Cotton Program selected FF&A to perform HVAC design on its most critical function – cotton classing labs - in 1985. Since that time, FF&A has designed 24 facilities that maintain very tight temperature and humidity constraints required to uniformly class cotton to ASTM standards. FF&A has been involved in every classing lab facility for the last 27 years. These projects have included troubleshooting existing labs, retrofitting and renovation of existing labs, and design and construction of new labs. FF&A is on the USDA Cotton Division team because of our expertise in psychrometric processes. This expertise is particularly valuable in humid climates in solving IAQ and mold problems in buildings. FF&A is the established expert in troubleshooting indoor climate problems and providing sustainable solutions that work.
The most recent project is the newly opened USDA Cotton Classing Facility in Lamesa, Texas. The $6M project is the worldwide standard for state-of-the-art cotton classing facilities.
The existing USDA Cotton Classification Facility in Lamesa, Texas was rebuilt from a structural shell and has been expanded to over 21,000 square feet and features state-of-the-art electronic cotton classification instruments, automation devices, rapid conditioning units, upgraded mainframe computer equipment, and energy conservation features not found anywhere else in the cotton classification industry. The facility will house up to 24 High Volume Instruments that can operate around the clock, when necessary, to provide accurate and timely cotton classification data to producers from the surrounding production territory. In addition to a completely new mechanical room and HVAC system, the renovated facility received a new oversized conference room for public presentations and use as well as new public and employee restrooms. Additional cotton sample storage and a new loading/unloading dock increase the capacity and capabilities of the lab. The $6 Million facility opened in September 2012.
This new cotton classing lab was designed to conserve energy. Some of the energy-saving measures that have been designed for the facility include a sophisticated control system for maintaining precise environmental conditions while using the least energy possible. The system is modular in nature so that the minimum amount of energy is expended in classing the crop. In the winter, a cooling tower cools water that is used to generate cooling through a heat exchanger, providing "free cooling" when the temperature outside is cold enough. Energy-efficient equipment is used throughout to minimize utility usage. Lighting systems are on motion detectors to conserve energy when the spaces are unoccupied. Cotton samples are moved to a baler by the use of a product-conveying air system, which includes condensers, drum filters, stripper fan, cyclone, and main fan. These components efficiently move the classed cotton to a fiber baler, where it is baled and loaded out with an automated baling system.
Client:
USDA AMS, Cotton & Tobacco Program
Year Completed:
Professional Services:2011
Construction: 2012
Project Size: 21,000 SF
Project Cost: $6M
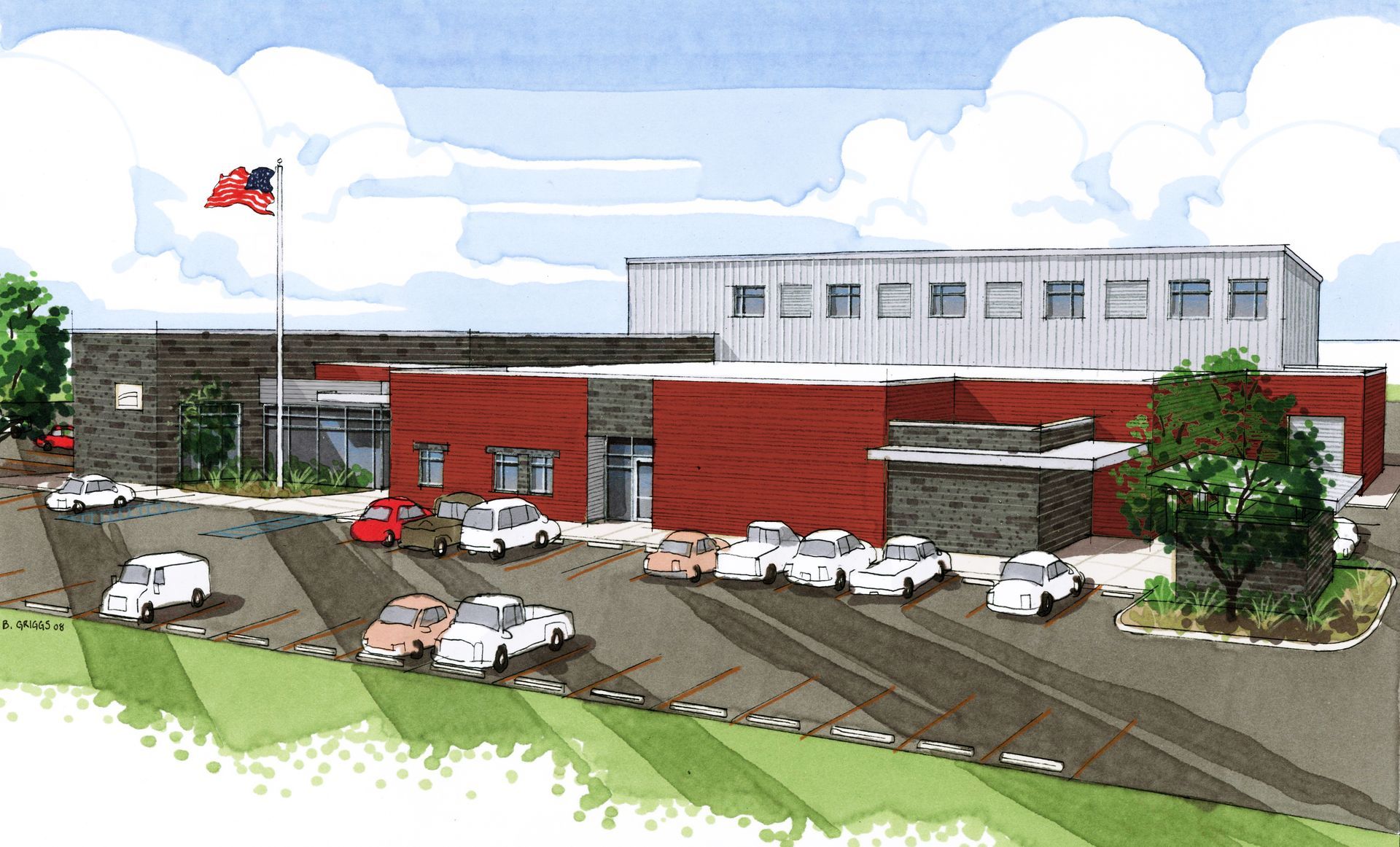
The City of Lubbock built a Biosafety Level Three laboratory in the existing health department building at 19th and Texas Avenue in Lubbock in 2002. The lab was inspected and certified for use by the Centers for Disease Control. In 2010-11, the City of Lubbock began a plan to close the health department building. In 2012 Texas Tech began planning to relocate the lab to The Institute of Environmental and Human Health (TIEHH) at Reese Center, Building 555. FF&A designed both the original Health Department BSL-3 laboratory and the new lab at TIEHH. The space consists of a clean and dirty ante rooms, a general lab and three smaller lab spaces. The biosafety cabinets are Type B2 and A2. The entire space served by a mechanical deck above the lab, which forms the containment barrier. The lab airflow control system is a Phoenix design with constant volume offset for all spaces. Supply air is HEPA filtered, and Exhaust air is filtered with a bag-in/bag-out HEPA filter housing located on the roof. Exhaust and supply fan systems are fully redundant and are on emergency power. Cooling is delivered by an air-cooled packaged chiller on emergency power, which is backed up by the TIEHH chiller farm. Ductwork is stainless steel and the system has been design for full decontamination using bio-seal dampers at each penetration through the containment barrier. A rooftop air handling unit is served by chilled water and heating water piping from a new mechanical room. The BSL3 lab and the mechanical equipment deck is fully sprinklered. Electrical components are served by a 450 KVA generator set located remote from the building.
Client:
Texas Tech University System / Perkins and Will
Year Completed:
Professional Services: 2012
Construction: 2013
Project Size: 44,284 SF
Project Cost: $2M
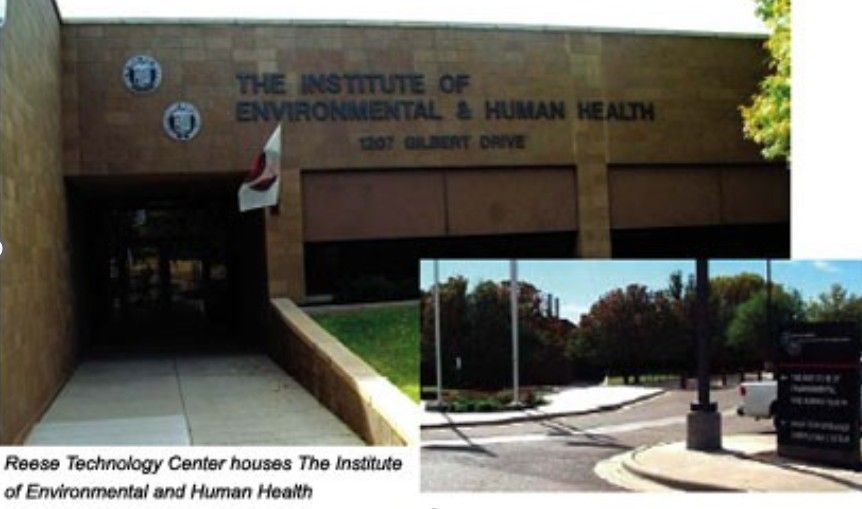
The Headquarters facility for USDA AMS Cotton and Tobacco was constructed in Memphis, Tennessee in 1992-1994. The facility includes CTP Administration, Memphis Classing Lab, QC Lab, and research and development of automation and cotton standards. As the equipment began to approach the end of its useful life of 25-30 years, some equipment was failing, including chillers, cooling towers, heat exchangers, boilers, and air compressors. It was critical that the solicitation of replacement equipment be configured to allow CTP maximum flexibility in project duration, efficiency, and cost. The contract documents were divided into bid packages that allowed CTP to consider the life cycle cost of the replacement equipment. Ultimately, one 200-ton chiller, one 200-ton cooling tower, one 90 HP boiler, and a 200-ton plate frame heat exchanger were replaced. The project was awarded within the available budget and within an acceptable schedule in June 2023. The project included an electrical design to support the replacement equipment. The project is under construction and will lead to greater reliability for CTP’s mission.
Client:
USDA AMS, Cotton & Tobacco Program
Year Completed:
Professional Services: 2023
Construction: 2023
Project Size: 80,000 SF
Project Cost: $1M
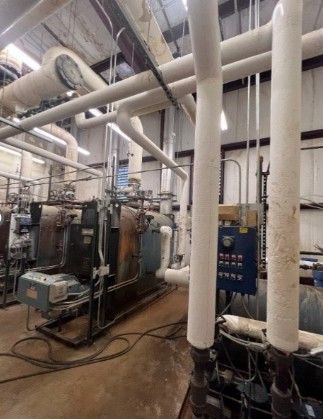
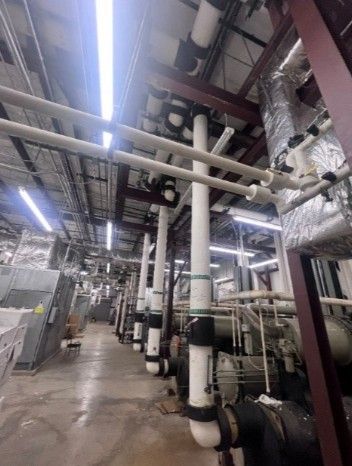
In March 2017 the CTP Deputy Administrator introduced FF&A to Cotton Incorporated. During a brief visit, Cotton, Inc. staff related their difficulty in maintaining ASTM conditions for their fiber research/classing laboratory. FF&A performed an on-the-spot analysis of the system. The lab was served by a packaged rooftop unit that was about four or five times too large for the application. The first-stage compressor was cycling over 50 times per hour. The compressors had been burning out and the tolerances were not being maintained. The information on how to improve the system was given verbally.
Subsequently, FF&A participated with the design engineers in several conference calls concerning the proper design of classing labs. After several conferences, Cotton Inc. opted to contract with FF&A to directly design improvements to the HVAC systems serving the Textile Service Lab, Spectroscopy Lab, Analytical Lab, Color Services Lab, and Finishing Lab. FF&A is under contract to design new controls and HVAC system components to ensure that the temperature and humidity ranges desired in the facility are maintained. The schematic phase of the project has been completed and options and costs presented for the scoping of the renovation. The next step in the process is to re-visit the site and begin contract documents.
To accurately control temperature and humidity, overlapping control ranges and equipment are required to provide smooth incremental cooling, heating, and humidification. Changes recommended to the system in Cary, NC include a new water chiller with capacitance tank and pumps, new air handling units with DDC controls, and reuse of existing steam humidifiers and reheat coils. The control system will be revised with new time-tested and proven sequences utilized by CTP Labs that will control the temperature and humidity within range. 4
The resulting project will reduce the installed capacity of the HVAC system from 120 tons of refrigeration down to 64 tons, resulting in a significant life cycle cost reduction in energy use. Maintenance that was being required every week will be reduced to normal routine preventative maintenance. The project has been scoped for $750,000 in construction and planning costs.
Client:
Cotton Incorporated
Year Completed:
Professional Services: 2017
Construction: 2017
Project Cost:
$750,000
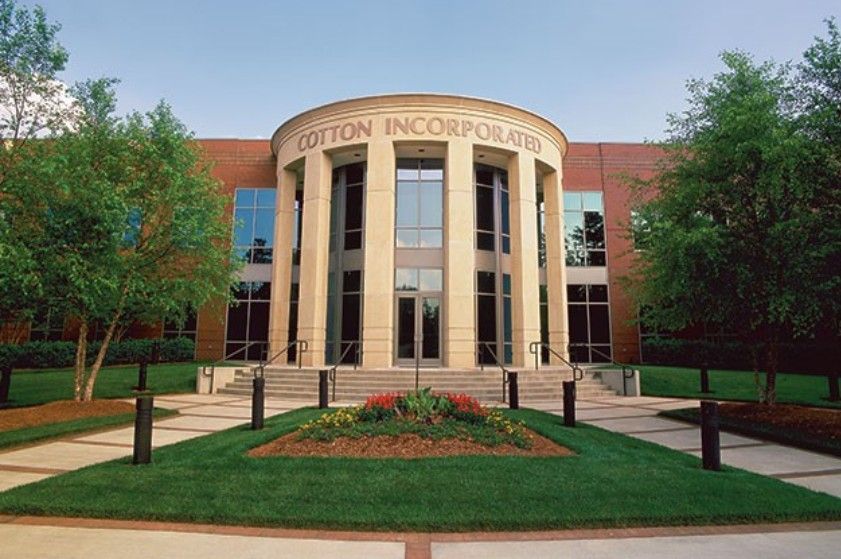
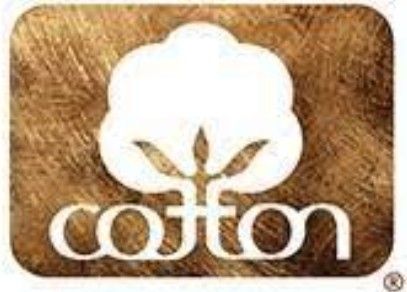
As the USDA AMS Cotton and Tobacco Program has evolved in its efficiency and consistency in classing cotton samples, most of the classing processes have begun to be automated by using conveyors, HVI vacuum systems, and other features of classing to improve the speed and repeatability of classing results. Labs in Abilene, Lubbock, Memphis, and Rayville have been automated using decoupled Color-Trash instruments. The remaining labs will be converted to automation gradually, as funds become available. Fanning, Fanning, and Associates and its consultants have designed all of the automation conversions of existing manual classing labs. Features required to support automation include improved flooring systems, conveyor layout and rough-in, compressed air piping, electrical outlets, and dust control air ducting for rapidly conditioning samples. The A&E team has worked closely with Steve Grantham and Roger Alldredge in the retrofit of these spaces to improve the CTP Classing Operation.
Client:
USDA AMS, Cotton & Tobacco Program
Year Completed:
Professional Services: 2022
Construction: 2019
Memphis Project Size: 4,300 SF
Project Cost: $1M
Rayville Project Size: 4,950 SF Project
Cost: $0.6M
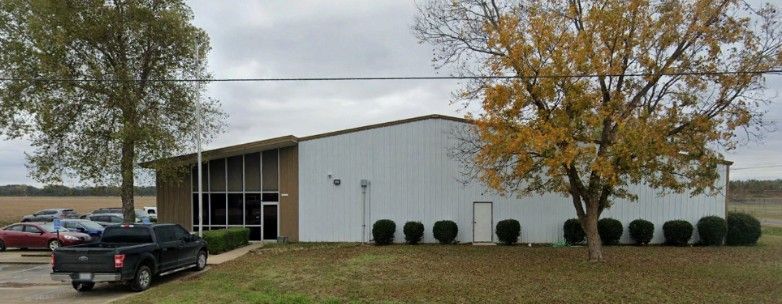
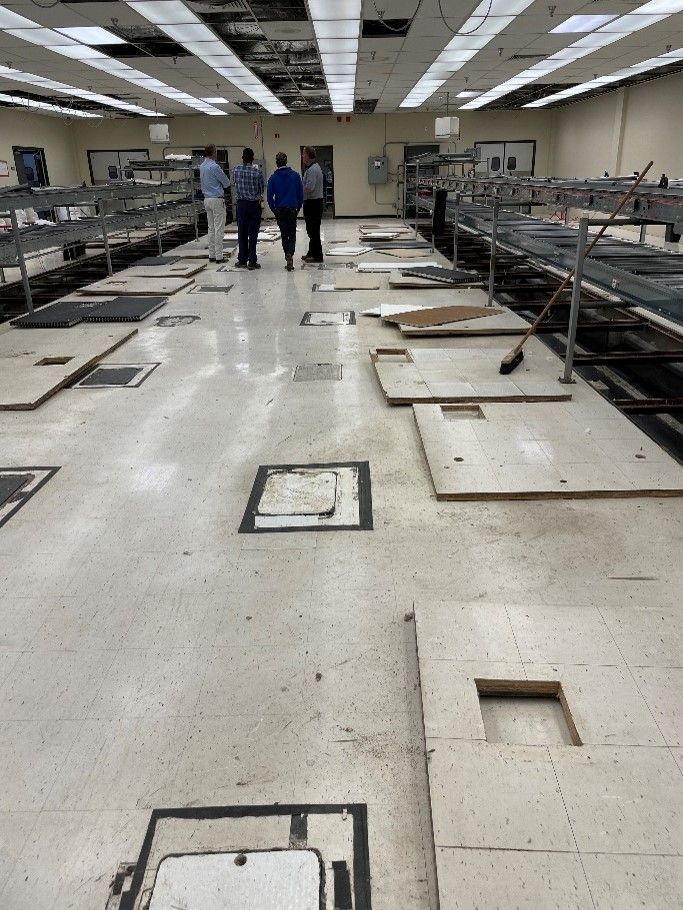
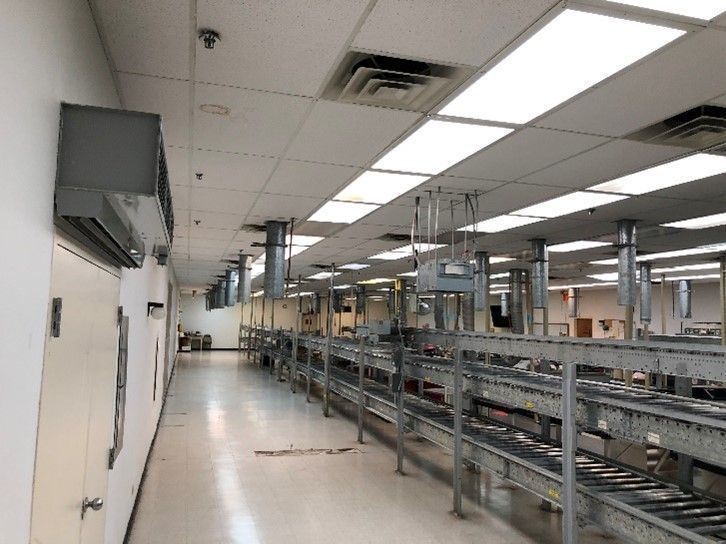
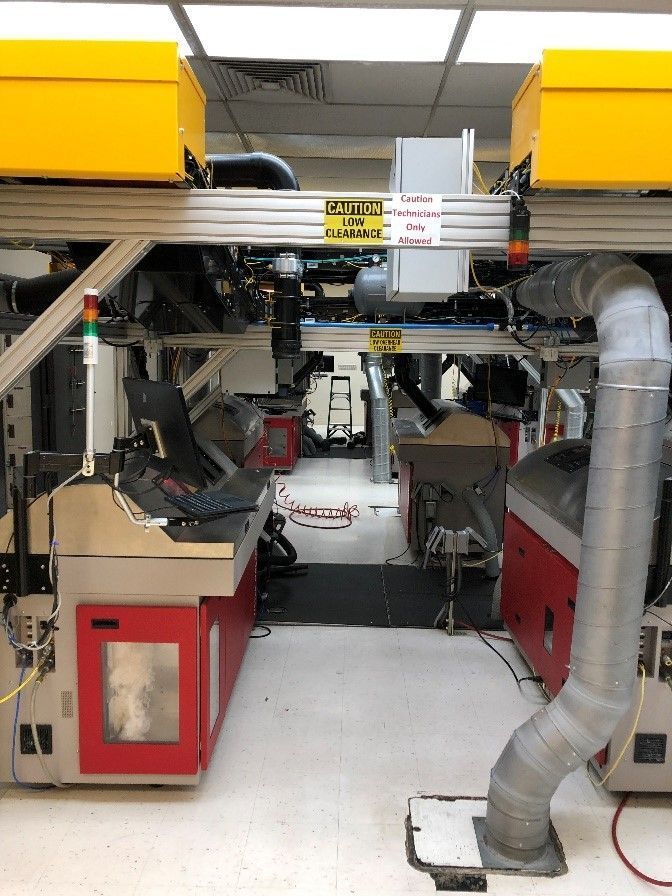
Generally, the building consisted of instructional classrooms, an auditorium, faculty offices, and some student gathering areas. Each area that had multiple occupants was equipped with a thermostat for individual room control. The comfort controls are sophisticated for the 21-SEER split system heat pumps, as they are part of the energy conservation strategy (VAV, humidity control) employed by the unit manufacturer. For the rooftop heat pumps serving the Auditorium, the BAS system manufacturer furnished digital thermostats that were adjustable within a range of the authority granted by the BAS front end. The override of the unoccupied mode button was included on the thermostats. Demand-controlled ventilation and a Dedicated Outside Air Unit with heat recovery were the centerpiece of this LEED Silver project. Electrical power used on site was generated by a GE wind turbine located behind the facility. A rainwater collection tank was utilized to store and use rainfall from the roof drainage system for irrigation on the site. The system is designed to use the 10,000 cisterns for capacitance between rainfall events for irrigation. The building HVAC and energy use systems were modeled using Trane Trace 700. The model was performed by another design team member, but verification and information that went into the model as gathered by FF&A. FF&A has Trane Trace 700 and has modeled HVAC system performance to comply with EPact 2005. FF&A maintained the USGBC website for the LEED Checklist pertinent to MPE disciplines. The building is now the showcase for the alternative energy program at Mesalands Community College.
Client:
Mesalands Community College
Year Completed:
Professional Services: 2011
Construction: 2011
Project Size:
40,200 SF
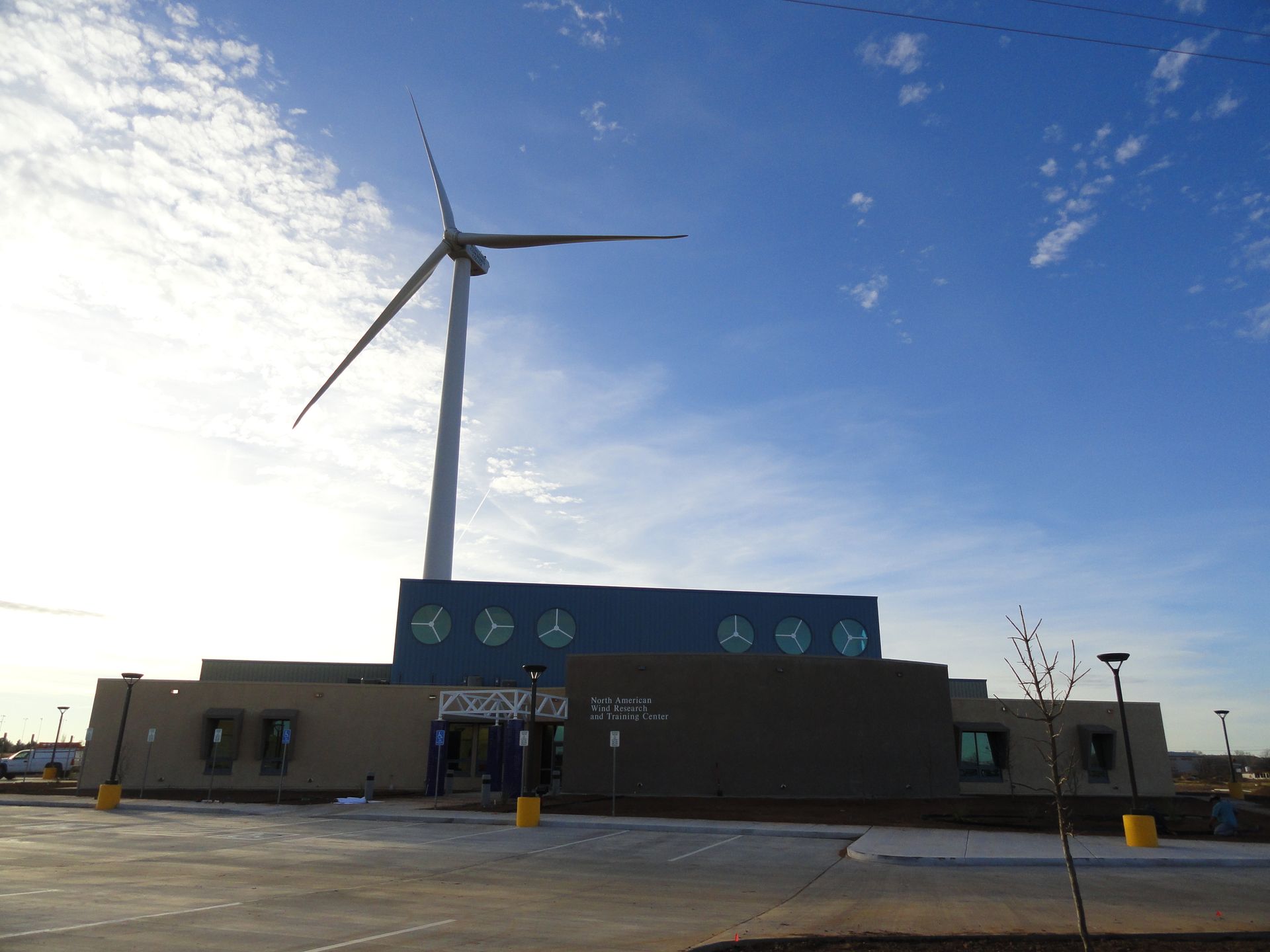
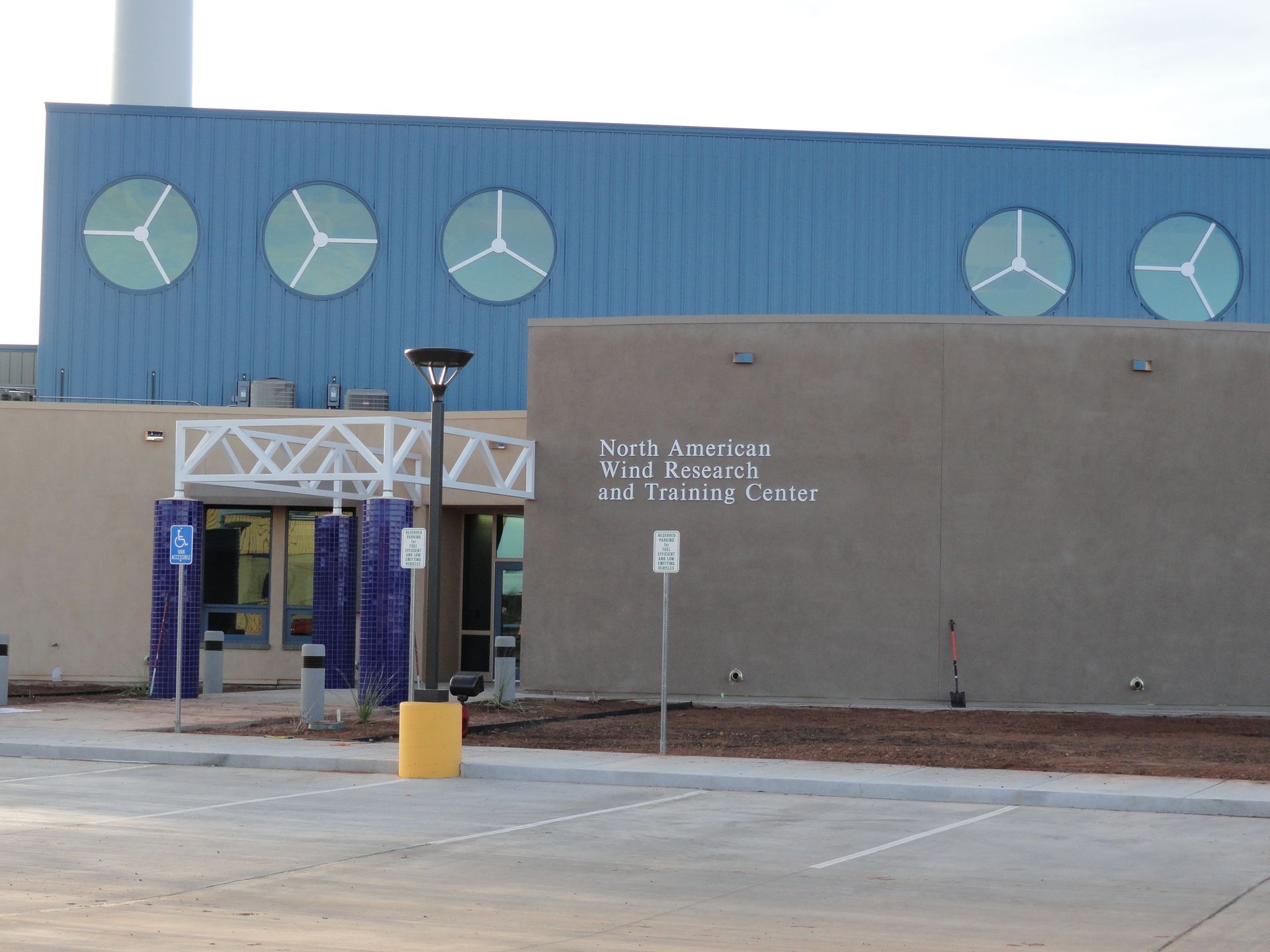
Share On: